10 月 . 11, 2024 20:00 Back to list
Choosing the Right Flooring Options for Your Commercial Warehouse Space
Choosing the Right Flooring for Commercial Warehouses
When it comes to commercial warehouses, the choice of flooring is critical for enhancing efficiency, safety, and overall operational success. Warehouses often experience high traffic from both heavy machinery and foot traffic, making the selection of an appropriate flooring material a fundamental decision that can impact everything from maintenance costs to employee safety. In this article, we'll explore the types of flooring options available, their respective benefits, and how to choose the best floor for your warehouse needs.
Types of Flooring for Commercial Warehouses
1. Concrete Flooring Concrete is perhaps the most common choice for warehouse flooring due to its durability and low maintenance. It can withstand heavy loads, resist spills from chemicals and oils, and is easy to clean. Modern advancements in concrete treatment have also made it easier to apply coatings that improve its slip resistance and aesthetic appeal.
2. Epoxy Flooring Epoxy is a popular option for warehouses that require a more decorative or slip-resistant finish. This polymer resin is applied over concrete to create a durable, seamless, and easy-to-clean surface. Epoxy flooring can also be customized with various colors and textures, making it visually appealing while maintaining functionality. It is especially beneficial in areas where spills are common, as it creates a non-porous surface that resists staining.
3. Vinyl Flooring Vinyl is another option that presents a softer and warmer feel underfoot compared to concrete. While often seen in retail or office spaces, high-quality vinyl can also find applications in certain warehouse environments. It's resistant to a variety of chemicals and is available in a range of styles and colors, making it versatile. Additionally, vinyl generally has better noise absorption characteristics than harder flooring options.
4. Tile Flooring Porcelain or ceramic tiles can be used in warehouses, especially in areas where hygiene is critical, such as food storage areas. They are easy to clean, water-resistant, and do not absorb odors. However, tiles may be less suitable for heavy equipment due to the risk of cracking under significant load.
5. Rubber Flooring Rubber flooring is well-known for its shock-absorbent qualities, making it an excellent choice for areas where employees may be standing for long periods. It provides cushioning, is slip-resistant, and absorbs sound, making it ideal in busy warehouse environments where noise can be an issue. However, rubber can be more costly than other options and may require more maintenance over time.
commercial warehouse flooring
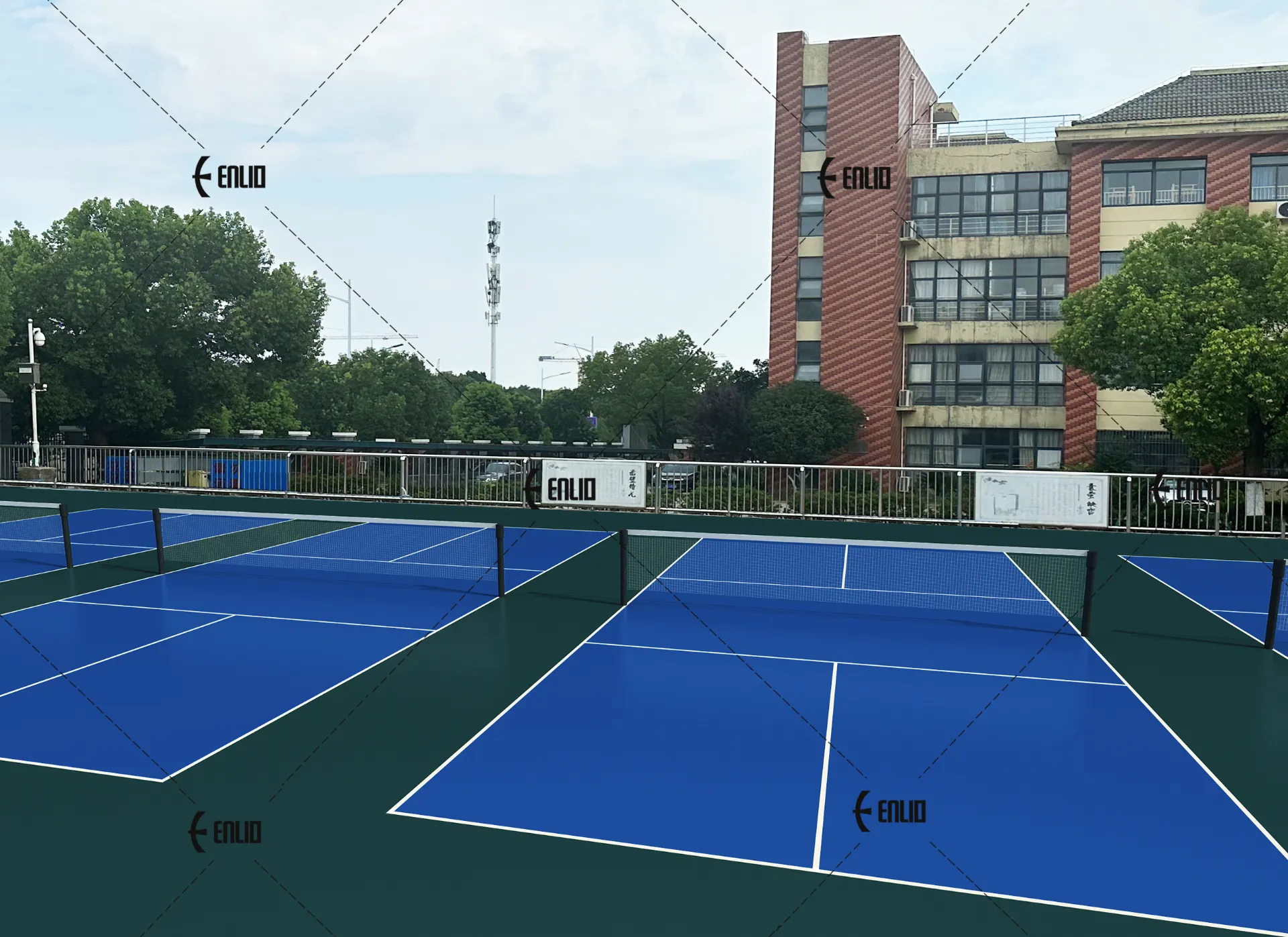
Factors to Consider When Choosing Warehouse Flooring
1. Traffic Volume and Load Capacity Assess how much foot and vehicle traffic your warehouse experiences. Heavy machinery requires flooring that can withstand significant weight without cracking or breaking. Concrete or epoxy flooring often performs well in high-traffic areas.
2. Environmental Conditions Consider the environmental conditions of your warehouse. If the area is prone to moisture or spills, selecting a non-porous material like epoxy or vinyl can help prevent damage and reduce cleaning difficulties.
3. Safety Requirements Safety should be paramount when it comes to flooring. Anti-slip surfaces are essential, particularly in areas prone to spills or where workers are frequently moving. Look for materials that offer good traction and consider applying slip-resistant coatings.
4. Maintenance Needs Evaluate how much maintenance you are willing to undertake. Concrete and epoxy often require minimal maintenance, whereas some softer materials like rubber may need regular upkeep to maintain their appearance and function.
5. Cost Budget is always a factor in flooring decisions. While cheaper options may seem appealing initially, consider the long-term costs that may arise from maintenance, durability, and replacement.
Conclusion
The flooring you choose for your commercial warehouse can significantly affect operational efficiency and safety. By considering the various options available—concrete, epoxy, vinyl, tile, and rubber—and evaluating factors such as traffic volume, environmental conditions, safety, maintenance needs, and cost, you can make an informed decision that suits your specific requirements. Investing in the right flooring will not only enhance the functionality of your space but also contribute to a safer and more productive working environment.
-
Custom Pickleball Court Solutions Convert Tennis & Indoor Builds
NewsMay.30,2025
-
Outdoor Pickleball Court Costs Build & Install Pricing Guide
NewsMay.30,2025
-
Premium Pickleball Sports Courts Custom Design & Installation
NewsMay.30,2025
-
Indoor Pickleball Courts Tennis Court Conversion & Custom Builds Tempe
NewsMay.29,2025
-
Professional Pickleball Court Installation & Tennis Court Conversions
NewsMay.29,2025
-
Grey Synthetic surface-rubber prefabricated track
NewsMar.07,2025